Uploading Files to Corel Then Laser Cutting
If you've e'er designed parts for 3D printing, simply want to explore what possible with 2d laser cutting and CNC machining, you're in the right place. Almost pop design programs take a 2D export option, merely each one is a lilliputian unique and may crave a few steps to get united states the best possible file.
With a little attending to item, your 3D designs can get perfect 2D files to use in laser cutting and 2nd CNC machining.
Start with the Correct Software
Using the right software is the most important part of the DFM (Blueprint for Manufacturing) procedure. Using software that is designed for 3D printers or 3D animation may non be optimized for 2D light amplification by stimulated emission of radiation cut or CNC machining.
Here'south a few of our favorite programs to use for 2d light amplification by stimulated emission of radiation cut and CNC machining:
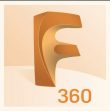
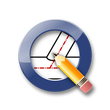
QCAD
Information technology's Free! – We honey QCAD for its simplicity, cost (gratis for personal apply), and information technology's well documented. (tutorial soon)
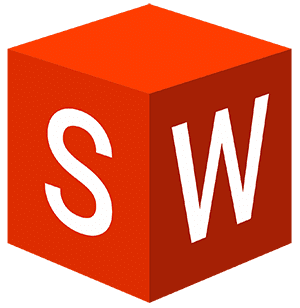
Some 3D-centric programs offer an option for 2D exporting, but they do not define 2D shapes accurately or efficiently. If yous're working in the following programs, your 2d vector files will likely not be optimized for laser cutting, and are non supported by our process:
- TinkerCad
- Rhino
- SketchUp
- VCarve
Ship Usa the Correct File Type
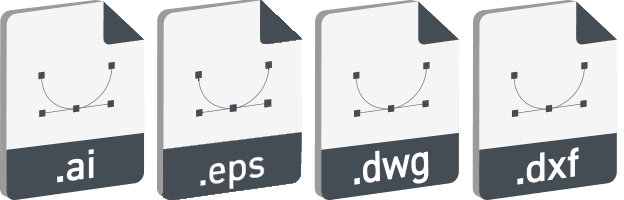
The software you apply will determine the file type that you transport to u.s.. The file types we accept are:
DXF – Exported from a sketch in Solidworks or Fusion360. Save-as from QCAD or other popular 2D CAD programs
DWG – Save-as from AutoCad, Revit, ArchiCAD
AI – Save-every bit from Adobe Illustrator only. If your program has an option to export equally an Illustrator file, but it's non Illustrator, try an .eps option instead.
EPS – Save-as from Adobe Illustrator or Corel Draw
Don't Use Conversion Apps
If your software doesn't save-as or export the common file types nosotros accept, that's a sign that there will be problems with the file you lot transport us. If you attempt to convert a file from 1 form to another using an online converter, app or plugin, weird things can happen. In about cases, the file volition not be useable.
Similar to human being language, the more you lot process a file through a digital translator, the less legible it will go (Google translate from English to Spanish then back to English to see what I hateful!).
Fusion360 and Solidworks: Focus on the Sketch
In Fusion360 or Solidworks, the first thing you do to create your part is make a sketch. For modeling purposes, you'll proceed to extrude, revolve or loft that sketch to make a fully formed shape. When y'all're designing for laser cutting though, the initial sketch might be all you need!
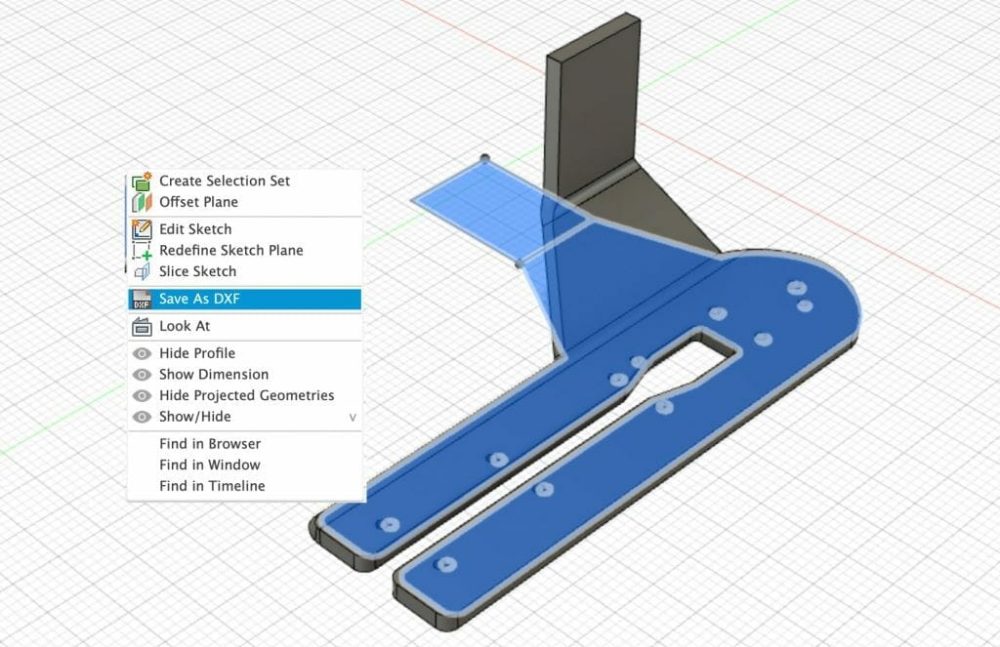
Learn more about how to create a DXF from a sketch in Fusion360.
Adobe Illustrator – Just Click relieve!
Although Adobe Illustrator doesn't support 3D design, information technology'due south nonetheless a bang-up tool for creating 2nd parts. If y'all designed your file in Illustrator, send united states the original .AI file. Please practice non export as a DXF, we have a special conversion process that we employ to retain the arcs and curves in your blueprint accurately.
Hither's a couple things to look out for to make the process easier:
- Remove guides
- Remove hidden layers
- Unlock all objects
- Remove devious points
- Utilise a single artboard
Designing for Light amplification by stimulated emission of radiation Cutting in Illustrator
Check Your Consign
If you lot view your DXF file in software like QCAD and it looks like in that location are more nodes than necessary, that'south a sign that your software didn't export the DXF correctly. We might be able to cut the parts for y'all, but the cutting quality will be reduced.
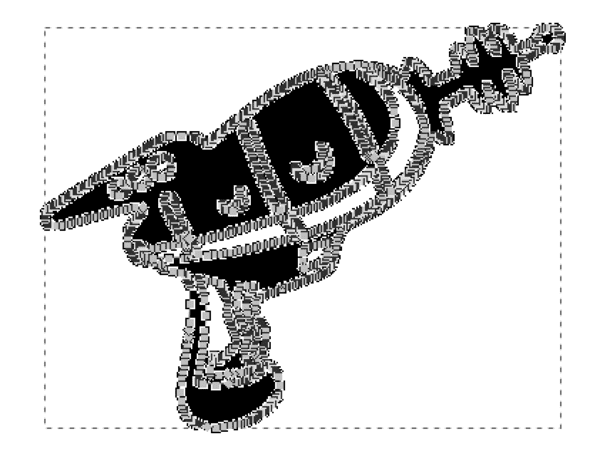
The light amplification by stimulated emission of radiation reads simple lines and shapes (we call the shapes "geometry") to decide the cutting path. All the geometry is defined past "nodes." Nodes are like a connect-the-dots game, and the laser volition happily get from one node to the next. Each node contains a set of directions, and can instruct the light amplification by stimulated emission of radiation to go straight to some other node or arc to another node.
If you're cutting a circle or hole in your design, there will be 4 nodes that define iv small arcs that make up the circle. The laser tin can read those instructions effortlessly, and the pigsty volition cut nice and polish. If your design isn't exported correctly, instead of smooth arcs, you'll get hundreds (or thousands) of tiny, straight-line segments and a ton of nodes. These extra nodes will result in rough or jagged edges on your function.
You're All Gear up!
Getting the hang of it? For tips on getting perfect exports every time in our supported software, we've got some handy tutorials here. Still non convinced why we're and then picky? Hither'south why we require vector files for laser cutting.
Source: https://sendcutsend.com/exporting-vector-files-from-3d-shapes-for-laser-cutting/
Post a Comment for "Uploading Files to Corel Then Laser Cutting"